

To begin weaving, the weaver dons the backstrap, which attaches her to the loom bar and tightens the warp. Its design dates back to precolonial times. The Yakan still use the primitive backstrap loom, which consists of different sticks and tangles of thread. In 2011, she assembled her loom and commercial cotton threads and put up her shop. She then decided to resettle in Mindanao to continue the weaving tradition. While on holiday in Zamboanga, Evelinda observed some stores offering beautiful Muslim crafts. Hence, from 2001 to 2011, Evelinda worked at a dispensary in Caif.
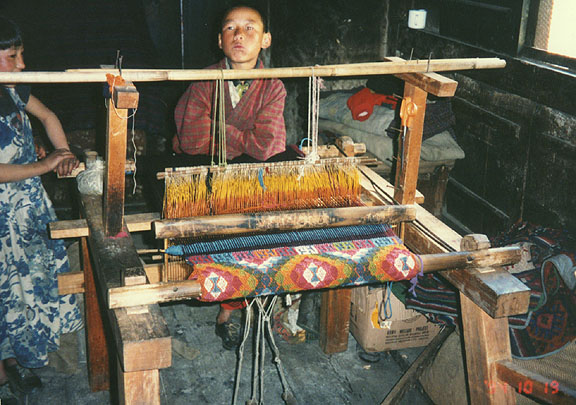
The requirement was a college degree and no license.

She learned from the Philippine Overseas Employment Agency that there was an opening for a medical technician in Saudi Arabia. However, the P30,000 fee for the review in Manila, excluding board and lodging, was steep for the family. To work in a hospital, Evelinda needed to take an examination for accreditation. In college, she took up medical technology at the University of Zamboanga under a scholarship of the National Integrated Study Grant Program. On weekends, she returned to the farm to continue weaving. In high school, she would stay at her grandfather’s house in Lamitan. At 7 years old, she produced coasters, eventually graduating to table runners and fabrics. Like most Yakan women, her mother stayed at home to weave.īy osmosis, Evelinda picked up the skill. Her father, a farmer, cultivated root crops, bananas and vegetables. Many settled in what is now called the Yakan Village.Įvelinda grew up in the boondocks, 15 km from Lamitan, Basilan. The military skirmishes in the ’70s forced them to migrate to Zamboanga. Her daughter, Olivia, is the fifth-generation weaver whose coasters are sold at Evelinda’s shop.Įvelinda will also pass on the craft to 18-month-old Princess when she’s 7 years old.Įvelinda recalls stories from her grandfather about how the Yakan came from Basilan. Her son Oliver, 21, graduated in customs administration. The earnings from her shop have put her children to school. It augments the income of herhusband, Ollie Hamja, a policeman. Weaving supported her education, and now her family. Many women are reverting to weaving,” she says in Tagalog. But when there was an epidemic in the trees, the Yakans could not subsist from it. “People were growing coconuts to earn money. The Yakan appreciate the economic benefits of preserving their weaving tradition and tribal identity. In other parts of the Philippines, weavers struggle to preserve their cultures despite poverty and exploitation. Lately, she has been outsourcing Yakan fabrics from her relatives so she can sew them into souvenir items. She also built a miniloom for her 13-year-old daughter, Olivia, who produces coasters. Some entrepreneurs buy either the fabrics or the souvenirs in bulk.Įvelinda, 44, spends four hours a day weaving Yakan textiles at home. Off-season, Yakans are lucky to get a couple of customers a week. The store also displays Tausug fabrics and Maranao brassware, woodcarving and chests. Her store offers woven pouches and wallets-the most saleable souvenirs-and tote bags.

Tourists have lauded the signature colorful geometric weaves of the Yakan, one of the 13 ethnolinguistic groups from Muslim Mindanao. Her eponymous shop, Tindahan ni Evelinda, is close to the Yakan Weaving Center along the National Highway, a must-see in Zamboanga City. The Yakan appreciate the economic benefits of preserving their weaving tradition and tribal identity.įourth-generation Yakan weaver Evelinda Otong Hamja still makes the basics of the traditional costume called semmek-the sawal or pants, the saputangan or the headdress/apron, the pinalantupan or sash, and the pis or the headscarf.
